Lo que conocemos como JIDOKA es una metodología que se originó por un japonés. Lo que se puede traducir como “Automatización de los defectos” o también como “Automatización con enfoque humano”.
Para conocer todos los aspectos relevantes de esta metodología lo único que tendrás que hacer es seguir leyendo este artículo.
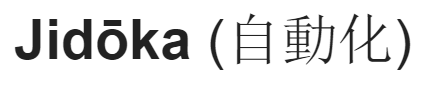
¿Conoces lo que es el método JIDOKA?
El método JIDOKA no es más que una metodología japonesa que se encuentra incluida en el Lean Manufacturing. El Lean Manufacturing puede ser traducido como “producción ajustada” y se encarga de mejorar la competitividad ayudando a crear el máximo valor añadido para los consumidores quitando actividades innecesarias.
Es entonces como el método JIDOKA tiene como finalidad que cada proceso tenga un autocontrol de calidad propio y se refiere primordialmente a los procesos industriales de producción a gran escala y también los procesos industriales de producción en línea.
Es entonces como este método funciona no solamente corrigiendo cualquier irregularidad puntual que pueda salir, si no también investigando cuál es verdaderamente la causa raíz de esta. Lo que permite entonces poder eliminarla y, en los mejores casos, permite también el permitir que esa irregularidad pueda repetirse en el futuro.
¿Cuál fue el origen del método JIDOKA?
El encargado de idear la metodología JIDOKA fue un japonés llamado Sakichi Toyoda, el cual inventó un dispositivo que fue capaz de detener un telar justamente en el momento en el que uno de sus hilos se fracturaba hasta romperse.
Pero no sólo eso, sino que también estos dispositivos tenían la capacidad de poder alertar mediante efectos visuales a la persona que se encargaba de operar la máquina que la misma se encontraba ahora detenida. Lo que significó entonces una reducción en los tiempos perdidos del proceso de producción. Al igual que dotar el mismo con su propio sistema de autocontrol.
¿Cómo ve el Lean Manufacturing el método JIDOKA?
Si nos enfocamos en el método JIDOKA desde el punto de vista del Lean Manufacturing se puede decir que su objetivo principal sería el de dotar a los procesos de producción de mecanismos de autocontrol de calidad, para que ante cualquier eventualidad que pueda suceder el mismo mecanismo pueda detenerse.
De esta manera se logrará entonces el poder reducir el número de unidades defectuosas que se pueden producir si el proceso sigue avanzando.
Es entonces como dentro del Lean Manufacturing se dice que el método JIDOKA es una metodología que puede recoger algunas particularidades de herramientas tales como son la Andon y también la Poka Yoke. Esto en función de que le sirvan como elementos de apoyo para poder lograr los objetivos por los cuales la implantan en los procesos.
Pasos del método JIDOKA
El método JIDOKA consta de los siguientes pasos:
Localizar el problema
Este es el primer paso a llevar a cabo en el método JIDOKA, en el cual se busca el poder detectar cuáles son los procesos que se encuentran intervenidos bien sea de forma automática por sensores, cámaras de visión o por algunas personas de forma manual.
Al hablar netamente de máquinas nos encontramos con que primeramente se debe implantar algún mecanismo que sea capaz de detectar posibles obstáculos para poder entonces detener la producción hasta que el inconveniente que ha sido encontrado pueda ser solventado. Por lo general estos inconvenientes se resuelven en muy poco tiempo.
Parar la producción momentáneamente
Este es el paso dentro del método JIDOKA que es incomprendido por la mayoría de las personas. Ya que estas tienden a pensar que se trata de detener a su totalidad el proceso de producción, pero hacer esto realmente es llevar a cabo mal el paso.
Lo que se busca al llevar a cabo una parada en la producción es distribuir en distintas secciones el proceso de producción para que, cuando se logre detectar un problema en una sección, la línea pueda seguir con sus funciones sin ningún problema mientras que el obstáculo o defecto logra ser resuelto.
Corregir el problema
Para continuar con el correcto proceso de producción debe implementarse un paso que sea capaz de corregir el inconveniente,.
En pro de que la producción pueda continuar de la mejor manera son utilizadas distintas opciones, tales como:
• La implementación de sistemas de señal por tarjetas. Conocido también como el método Kanban.
• El insertar una unidad de estación que se encargue del Re-Trabajo.
• Detener completamente la producción hasta que se logre solventar la avería.
Investigar cuáles son las causas y diagnosticar el problema
Este es el cuarto y último paso para llevar a cabo de manera correcta el método.
Después de localizar cuál ha sido el origen del problema se podrá comenzar a trabajar para lograr establecer una solución que no permita que se repitan estos problemas u otros similares durante el proceso de producción.
Sistemas de detección
El método JIDOKA se basa en dos sistemas de detección
Capacidad del operario de máquina de parar la producción
Es en este caso donde el mecanismo que detiene y logra prevenir la producción de las unidades defectuosas que se interpretan como pérdidas pueden ser accionados por las personas operario de la planta de producción. Es decir, cuando el trabajador reconoce que se debe llevar a cabo un paro.
Máquinas automatizadas
Estas son las máquinas que cuentan con dispositivos de detección automáticos para así lograr prevenir, en el proceso de producción, que se dé como resultado unidades defectuosas que suponen pérdidas para cualquier empresa, fabricante y cliente. Entre ellos se encuentrans sistemas de visión artificial, detección de cotas, colores etc y sistemas de rechazo automático.
En cualquiera de los dos casos nombrados anteriormente, pertenecientes al método JIDOKA, la herramienta de Lean Manufacturing, Andon, juega un papel importante. Debido a que después de detenerse la operación es importante que todo el proceso se alerte mediante una señal luminosa fácil de identificar.